The aim of the joint project is to reproduce the actual flow conditions in the fluid of working energy saving devices (ESDs) and propellers in detail so that the numerical methods can be used with sufficient accuracy for engineering applications and at an industrially justifiable cost. Based on the assumption that the insufficient detection of the instationarity of the flow in the stern area of a ship is the cause for the lack of forecasting accuracy, experimental and numerical methods are to be developed that allow the detection of turbulent flow fluctuations in the area of the stern flow and their effects on ESDs.
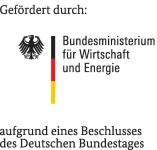
Title: | Hydrodynamic prediction and evaluation of realistic loads on ESDs SVA: Development of a measurement and scaling procedure for realistic prediction of transient forces on energy saving devices |
Term: | 10/2019 – 09/2022 |
Project Manager: | Pascal Anschau |
Founding: | Federal Ministry for Economic Affairs and Energy |
Project administration: | Project Management Jülich |
Partners: | IBMV, MMG, Uni Rostoc |
Reg.-No.: | 03SX493C |
The laboratory investigations, which will be carried out with two methods, optoelectronic and electromechanical, aim to develop measurement methods for high-frequency measurements of the force and pressure fluctuations on ESDs caused by turbulence and to provide measurement data for the validation of the numerical simulation method to be developed. The optoelectronic method to be used is a high-speed PIV (Particle Image Velocimetry) method. This will be used to investigate the flow around the ship’s stern and in particular the inflow and outflow of the ESDs. The electromechanical investigations are aimed at the high-frequency recording of the transient force and pressure fluctuations at the ESDs and in the propeller bearing on the model. A new measurement system is to be developed for measuring the forces at a wake equalizing duct, which allows the temporally high-resolution registration of all three force components and the pressure at the ESD; in addition, the radial propeller bearing forces will be recorded. The data generated in this way will provide insight into the pressure and force effects of the turbulent flow fluctuations.
Numerical simulations are carried out to determine the transferability of the model test results to the full-scale ship. The simulations will be validated with the corresponding measurement results. These investigations will initially lead to a procedure concept with which the force and pressure fluctuations at the duct can be transferred from model scale to the duct in the full-scale version. For the development of the scaling procedure, investigations will be carried out on different scales. A hybrid method to be developed is to be used for the simulations. From the simulations with different scales, it should be possible to make a statement about the size of the load peaks to be expected at the duct in the full-scale version, possibly also a statement about the probabilities of occurrence.